Behind the Scenes: Spy House Production (1)
This is a sharing of making a spy house with 3ds Max, provided by Fox Renderfarm, your TPN-Accredited 3ds Max render farm and cloud rendering service provider. The main software used in this article is ZBrush, Marmoset Toolbag 3. The following is the final effect display, then share the overall production process.
Goal Setting
First of all, this project uses the standard game production process, using 3ds Max to complete the basic Polygon construction, and part of the production of Hight Polygons, and ZBrush completes the carving of local Hight Polygons, Marmoset Toolbag 3 baking, Substance Painter, complete the production of the PBR material, and finally use Marmoset Toolbag for rendering.
After the above process is established, production begins,
In the Low Polygons stage, Polygon is started according to the angle of the original painting, which is convenient for establishing the scale of the model.
After the Low Polygons are completed, in order to facilitate the unification of the material style, the production of the Middle Polygons, High Polygons is completed according to the material.
Production Process
- Modeling
- Material production
- Marmoset Toolbag rendering
Modeling
First of all, there is an iron table in the center of the scene, so we first set the height of this table as the scene height reference, the table height is set to 1.3m, and then complete the Low Polygons in 3ds Max.
After Low Polygons is completed, put the models together, and adjust the size and distribution of each model.
It is established that the proportion position of each part of Low Polygons is correct, and some details can be added to the model. There are a lot of reusable objects, we have added different details to them so that the repetition is not too high.
Taking these metal boxes as an example, adding different details to them can better reduce visual duplication.
Here takes one of the metals as an example to share the production process:
After Low Polygon was completed, it began to add details, and then the model was UVS split:
Points to note:
We made the prototype groove on the surface so that when making materials, we can use the intelligent mask to calculate the paint and stains, reducing the workload. When making circular grooves, pay attention to controlling the number of lines according to the size of the circle, and try to make Low Polygons and High Polygons match each other when baking to produce a good normal map.
When making the lampshade, the glass cover is a Geosphere, to avoid a strange texture when the glass cover reflects.
After selecting the sphere, click Hemisphere to get a hemisphere, so as to avoid the generation of strange textures, and then use the zoom tool to adjust the size ratio.
The edges of the sphere need to add lines to avoid the deformation of the model and check for useless points or lines.
High Polygon Production
It is not difficult to make the metal part Hight Polygons. The edge position needs to add lines to avoid model deformation. Add a turbo smooth modifier to check if there is any deformation. If there is any adjustment, adjust it again.
Low Polygon Production
Directly use the Hight Polygons made by Turbo Smooth, directly reduce the surface based on the model with added details, delete the lines that do not affect the structure, and use the options in the graphite tool to check whether there are polygons.
Make the Low Polygons of the sofa, make the basic shape of the sofa in max, and then sculpt the High Polygon in ZBrush, and then use the topology tool to complete the Low Polygon. Note that the place close to the 90-degree angle must distinguish between the smooth group and the cut-off UV.
The sofa Hight Polygon is completed in ZBrush. When sculpting, different wrinkle effects should be added according to the different materials finally presented. As shown below: a relatively hard leather sofa, the folds are mainly distributed at the stitches, and there will be no large and wide folds. The surface of the seat cushion will be slightly concave and convex due to long-term use, and the foot cushion and the bottom of the armrest near the place will be slightly slack. The stitching of the sofa is not easy to be too neat, and a little curvature will appear more natural.
Baking Normal
Baking uses Marmoset Toolbag 3, of course, there are many other ways, you can also use Substance Painter and ZBrush baking normal. But the advantage of choosing Marmoset Toolbag 3 is because we intuitively modify the normal.
The following figure is a basic introduction to the baking normal of Marmoset Toolbag 3:
Next is the normal modification panel:
Recommended reading
Top 9 Best And Free Blender Render Farms of 2025
2024-12-30
Revealing the Techniques Behind the Production of Jibaro "Love, Death & Robots", Which Took Two Years to Draw the Storyboard
2025-02-10
Top 10 Free And Best Cloud Rendering Services in 2025
2025-03-03
Top 8 After Effects Render Farm Recommended of 2025
2025-02-10
Top 5 Best and Free 3d Rendering Software 2025
2025-02-10
Shocked! The Secret Behind Using 3D to Make 2D Animation was Revealed!
2025-02-10
How to Render High-quality Images in Blender
2024-12-04
Easy Cel Shading Tutorial for Cartoon in Blender Within 2 Minutes
2025-02-10
Partners
Previous: Behind the Scenes: Spy House Production (2)
Next: The Witcher 3 Character Model Making Process
Interested
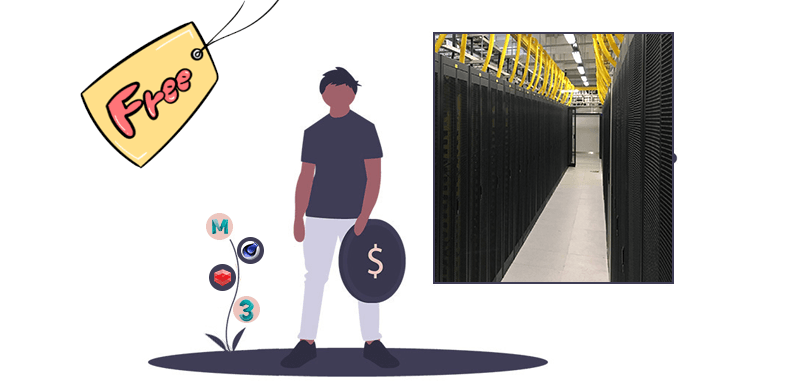
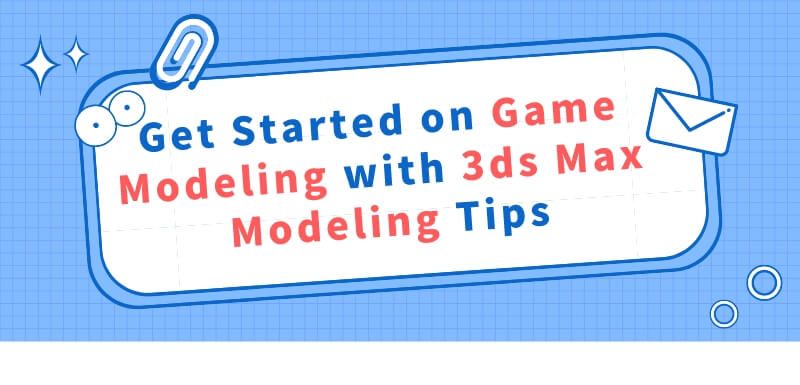
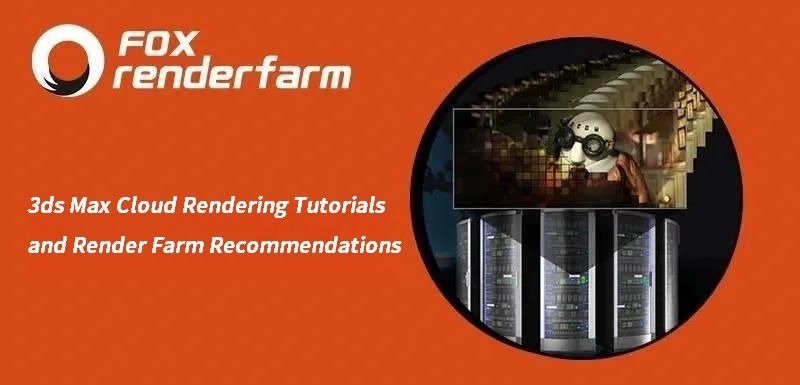