3D Modeling Tutorial: Handheld Fan
In this article, the best CPU & GPU could rendering service provider, Fox Renderfarm, will share with you a 3D modeling tutorial about how to make a handheld fan.
Hi, I am Resh, a 3d artist, before making the handheld fan model, we need to observe its structure and composition. The overall shape of the small fan is relatively simple, the lines are relatively smooth, and the modeling is not difficult. All the steps are simple. Tool of.
Because there are no three views with a suitable angle, we can use the Snipaste screenshot tool to put the reference image in the production software, adjust the size and place it in a suitable position.
First, start modeling from the head of the small fan, locate the centre point to the coordinate origin and draw a circle, (note that it is best to hold down the shift key when drawing a circle to avoid the drawn entity seam line being chaotic, which will affect the modeling and aesthetics), extrude the entity along both sides, and adjust the uniaxial scaling to the appropriate width.
Use the shell command to shell the cylinder, and copy a circle of edge lines to offset the curve inward.
Use the offset curve to extrude the entity, adjust the position, and use it to perform Boolean difference for the thin shell.
Use the curve function to capture the top and side points to draw a curve, and to adjust the corner radian of the curve.
Rotary forming and offset by a thickness (the thickness of the offset is the thickness of the inner ring of the cylindrical shell)
Next, to do the part of the grille, first draw a rectangle with the centre point. In order to achieve up and down symmetry, first, array 7 equal parts upward, and then mirror the upper 6 parts of the X-axis to arrange the shape.
Use these rectangles to extrude the solid and perform Boolean subtraction to get the shape shown in the figure below.
In order to avoid the edge of the model after cutting and increase the difficulty and workload of chamfering, you can first chamfer the inner and outer edges of the back, and then make a backup copy (which will be used later), and then take it out. The rectangle of the previous array, as before, adjusts the position for the Boolean difference set.
Take out the backup, draw a rounded rectangle and extrude the entity for Boolean segmentation, delete the redundant part, the obtained shape is as shown below, adjust the position and perform a Boolean union with the grille, so that our entire grille has a boolean union. The styling is done.
Next, we will make the fan blade inside, first, locate the centre point to the origin to draw a circle and extrude a small cylinder on both sides, then copy a circle of edge lines, offset the curve inward, (for the convenience of observation and operation, you can let it is displayed separately).
Extract the surface and split it with the offset curve, then blend the surfaces.
Draw a rectangle, then close the curve raw surface, rebuild the surface and adjust the shape.
Then offset a suitable thickness, round the top two sharp corners, and then adjust the position as shown in the figure below.
Then capture the centre point of the cylinder to make 7 copies of the circular array, and then the Boolean union is completed, and the fan blade is completed; then the mesh cover of the Boolean union is also unioned.
Next, start to model the fan handle below, and draw an ellipse in the top view to capture the origin, still extruding the entity, the size and length can be slowly adjusted according to the reference image, and then use the grille to perform Boolean difference set on it (delete Enter the object and select No), and then delete the redundant part.
Draw a straight line and pull out a surface, adjust the height according to the reference picture, and cut out the parting line by Boolean division of the fan handle.
Next, make the buckle at the connection of the fan handle, first hide the cylinder below, and draw an ellipse and two rectangles at the bottom of the upper section (the rectangle can be drawn on one side to maintain symmetry and then mirrored on the Y-axis), Then stretch out the corresponding length according to the reference drawing.
Take out the cylinder that was hidden, perform a Boolean difference set on it with the three parts just extruded (delete the input object and select No), get the groove as shown in the figure below, and then hide other things.
Switch to the front view and draw such a curve, then pull out a surface and mirror it, and then do a Boolean difference.
Then bevel this edge to get this shape.
Then take out the two small cubes that were just hidden, select these two faces on both sides, and pull them out a little to satisfy the shape. Because it is a buckle, it can only be fastened when it protrudes a little.
The three components Ctrl+shift single-select the top and stretch the handle of the upper half to Boolean division.
Draw a right-angled line, pay attention to the height of the line, to avoid that the cut shape will pass through the mould, then pull out a face and mirror it, and then display the two cuboid parts separately, you can slightly adjust the faces on the left and right sides, to make it cut out to look more beautiful and more in line with the shape of the reference image; then perform a Boolean difference set.
Next, go to the modeling of the shape at the bottom of the fan handle, copy a circle of edge lines to offset inward and extrude the entity, and then perform a Boolean difference set on the upper part for the lower part
Copy a circle of edge lines to offset the curve inward, then extract the surface, divide the surface with the offset line and delete the excess, then move it up a little to form a height difference, then loft the raw surface, and then combine. Take a look at the surface.
Then take out the grille and the upper part of the handle for Boolean union, then we make a parting line, draw a straight line from the middle of the side, and stretch a small thickness on both sides for the Boolean difference.
So far, the whole product is basically finished. Let's do some details on the chamfer and some button logos. Except for the part of the grille, the chamfer can be poured out without any pressure using the rounding command.
The position of the button can be extruded into a body by drawing lines and chamfered after Boolean division. There is also a Type-c interface, which is also drawn and then divided by Boolean and then chamfered.
In the LOGO part, you can use one-click LOGO text, or use the text tool and then Boolean segmentation, and then chamfer.
In the LOGO part, you can use one-click LOGO text, or use the text tool and then Boolean segmentation, and then chamfer.
Recommended reading
Top 9 Best And Free Blender Render Farms of 2025
2024-12-30
Revealing the Techniques Behind the Production of Jibaro "Love, Death & Robots", Which Took Two Years to Draw the Storyboard
2025-02-10
Top 10 Free And Best Cloud Rendering Services in 2025
2025-03-03
Top 8 After Effects Render Farm Recommended of 2025
2025-02-10
Top 5 Best and Free 3d Rendering Software 2025
2025-02-10
Shocked! The Secret Behind Using 3D to Make 2D Animation was Revealed!
2025-02-10
How to Render High-quality Images in Blender
2024-12-04
Easy Cel Shading Tutorial for Cartoon in Blender Within 2 Minutes
2025-02-10
Partners
Previous: Enter to Win Grand Prizes and Grab a Chance to Create Fox Renderfarm Mascot
Next: Get an Extra $50 CPU Render Coupon from Render Farm Now!
Interested
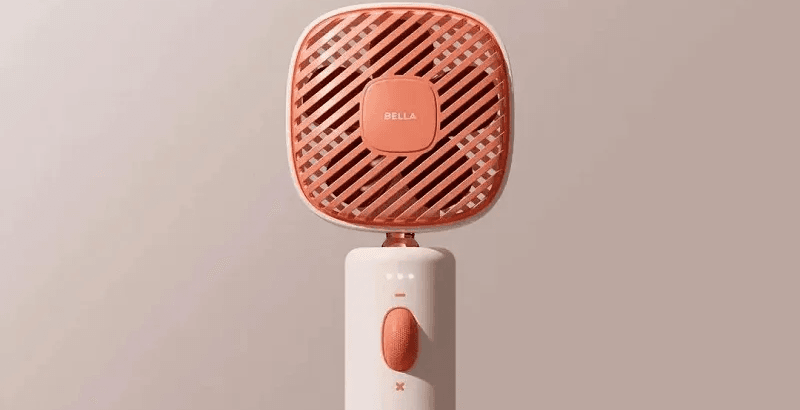
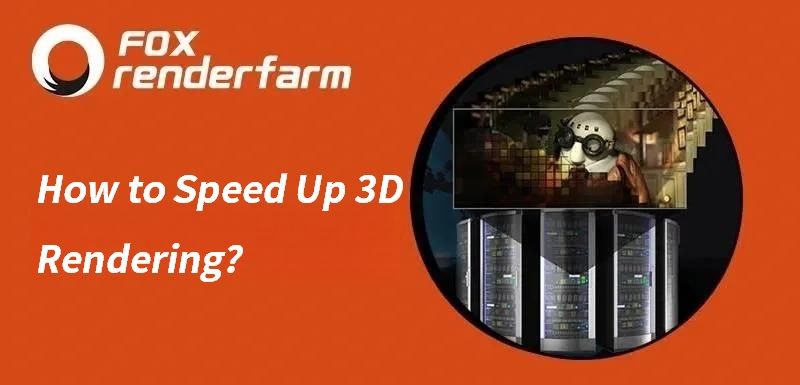
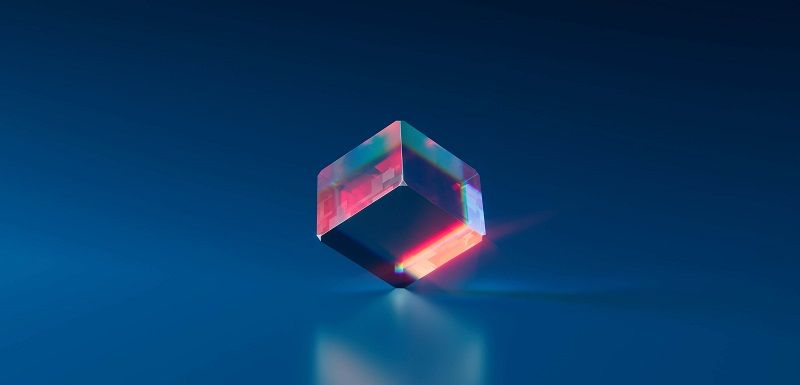