Fox Renderfarm Blog
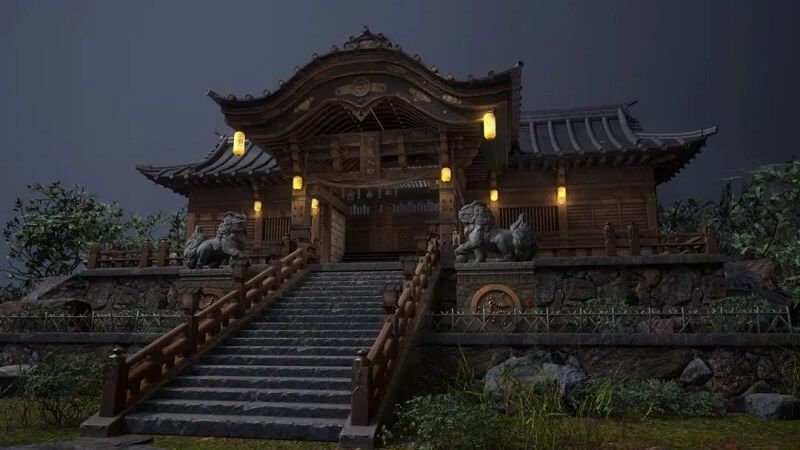
How to Create the Entrance of 'For Honor'
3ds Max Tutorials
The leading cloud rendering service provider and render farm in the CG industry, Fox Renderfarm, will show you in this post a scene inside "For Honor," the Entrance, created by a student who is learning 3D modeling. The creator completed this work over a period of four weeks by solving problems and challenges with the help of his/her teacher and his/her own efforts. This article is a summary of his/her experience in the creation of this scene.Final result:Analyzing Concept Art &x26; Building Rough ModelsThis is a case of the PBR workflow, specifically utilizing 3ds Max for low-poly modeling, ZBrush for high-poly sculpting, TopoGun for retopology, Substance Painter and Photoshop for texture, and ultimately rendering with Marmoset Toolbag 4.To ensure production progress, in the early stages, the scene was initially constructed in 3ds Max based on the concept art as a large-scale reference for proportions, and then the actual production process began.Rough modelMaking Mid-poly ModelsHouse Structure: serving as the foundation of the scene framework. The house was divided into several parts for construction, including the roof, walls, floor, door frames, steps, and two side stone platforms. Through analyzing the concept art, it was determined that the stone walls and roof tiles employ a repeating texture pattern, which was subsequently applied throughout the scene.The scene props included stone lion statues, lanterns, ropes of hanging tassels, and more. Among them, the stone statues, steps, and several wooden elements were sculpted using ZBrush.The process of creating the mid-poly model involved continuously refining and adding more intricate details based on the rough model. It was important to analyze which models require sculpting and retopology during the initial stages of production, and which models could be reduced in detail to serve as the low-poly model. Conducting this analysis early on significantly improved efficiency in the production process.Mid-poly modelMaking High-poly ModelsThe high-poly modeling stage was relatively intense, involving numerous wooden doors, plaques, walls, as well as stone steps and statues. However, the task became less laborious when it came to identical wooden boards in the scene, as they could be easily adjusted and reused.Statue sculpting:Since the only element in this scene that required complete sculpting was the stone lion, I decided to challenge and improve my sculpting skills by starting from a sphere. After several days of sculpting, I began to see some progress. Then, with guidance from my teacher, I delved deeper into proportions, structure, and finer details.Props sculpting:The wooden boards, during the sculpting process, were meticulously sculpted stroke by stroke to enhance the texture and bring out the grain. Additionally, props like stone steps were also carved.Afterward, the UV unwrapping and baking process followed.Making Low-poly ModelsIn the early stages, we conducted an analysis of the assets. Among them, only the stone lion required retopology, while the remaining props could be obtained through reducing the mesh of mid-poly models.Overall, retopologizing the low-poly model is a relatively simple but patient task. There are several points to consider during the process: 1. Controlling the polygon count of the model. 2. Planning the mesh topology in a logical manner and determining whether certain details need to be retopologized. 3. Evaluating the density of the mesh topology for proper distribution.During the low-poly retopology stage, we encountered few difficulties. We followed a standard of 1m³/512 pixels to create the textures and planned them accordingly based on the predetermined pixel density. Then, we proceeded with UV unwrapping and layout. Throughout this process, we encountered issues such as seams appearing and models turning black. Eventually, we identified the problems as certain areas of the model lacking smooth group separation in the UVs and flipped normals. When placing the UVs, it is important to fully utilize the UV space to avoid wasting resources. Additionally, we needed to redo some of the UV work later on. It should be noted that in 3ds Max, when using automatic smoothing groups, it may not be apparent if the normals are flipped. Therefore, it is advisable to double-check after completing each section.Next was the normal map baking. We matched the high-poly and low-poly models in 3ds Max and ensured that there was some distance between all the models to avoid overlapping during the baking process. If any issues arose with the baked normals, we would repair them in Photoshop. Fortunately, there were no major problems throughout the entire baking process, so minor adjustments in Photoshop were sufficient.Low-poly modelMaking MaterialsI initially conducted material rendering for the sculpture and showed it to my teacher. However, the teacher pointed out some shortcomings. With guidance from the teacher, I gained a new understanding of material rendering. The key is to focus on volume first and then details. Volume here does not solely refer to the presence of volume under lighting conditions, but also the perception of volume even in the absence of lighting, relying only on colors. The addition of darker shades and textures further enhances the sense of volume in the model. Finally, sharpening was performed to make the details more prominent. By following this approach, the materials created would appear three-dimensional under lighting effects.RenderingAfter completing meticulous file organization, I standardized the naming of models, material spheres, and textures. This significantly reduced the workload when using Marmoset Toolbag 4. Once all the preparations were done, I began placing the models, setting up the lighting, adding special effects, and finally positioning the camera for rendering. During this process, a considerable amount of time was spent on lighting. The coordination between model materials and lighting never seemed to achieve the desired effect. However, with guidance from my teacher, I was able to improve the overall result.The above is our experience sharing the production process of the Entrance for the game "For Honor".Source: Thepoly
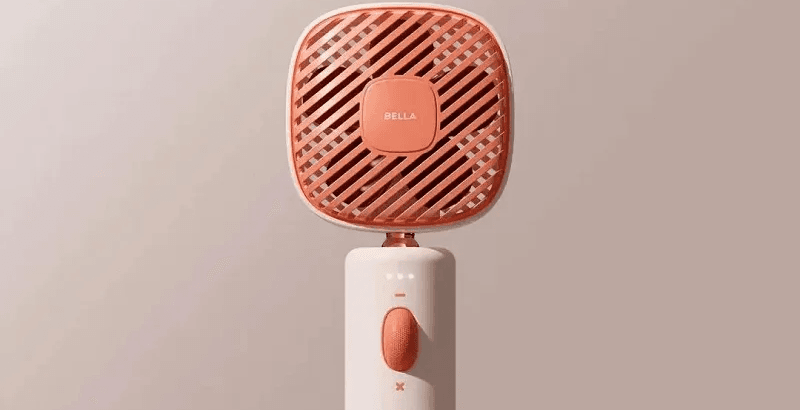
Learn How to Make a Handheld Fan in 3D
3D Tutorial
Today, Fox Renderfarm, the industry's leading cloud rendering service provider and render farm, will bring you a 3D tutorial that explains how to make a handheld fan. Let's get started right now.First import the image, use the straight line tool to draw the length of the handle, then use the rotational molding tool to create the handle and add a cover.Generate a rectangle using the center point, adjust it to the appropriate size, and then generate a circular runway. At this point, use the fitting tool to get the appropriate shape.Select the circular runway that was just generated, hold down Shift to extrude the faces on both sides and add a cover, then use the shell tool to shell both sides.Copy the inner edge line of the shell, extrude the face and add the cover, pull off the inner face to keep only the outer side, and then chamfer to generate the outer layer of the shell that needs to be hollowed out.Use curves to draw the edge shape of the connecting axis, then use rotational molding to generate the surface, and then add the cover to generate the solid.Connect the rectangle diagonal, use the diagonal to generate a round tube, and adjust the angle and thickness of the tube so that the angle and thickness of the tube match the reference picture.Draw a diagonal line again and use the Line Array tool to array along this line, where the number of arrays is 18.Use the object intersection line function to select the round tube and the shell to be hollowed out, determine whether the position matches by the object intersection line, adjust the position and then cut to get the hollowed out object.Use the Rectangle tool to generate a runway circle, adjust it to the right size, then cut and combine it with the hollow object and offset it inward to get the solid. The same can be done for the outer runway circle, here you need to make a copy of the hollow object for backup.Use the mirror tool to mirror the hollowed-out model made in the previous step to the back, then use the method in the fourth step to get an unhollowed-out shell, generate a rounded rectangle and cut it according to the second reference picture, then use the combination tool to combine, and finally offset the surface to get the solid.Use a rectangle to frame the size of the button, then use a straight line to connect the midpoint of the rectangle, next use the center point tool to generate a circle, and squeeze the circle to the right size and adjust the height of the button.Split the button and the handle for spare, and then chamfer the top of the handle for the next step.For the base, again using the rotational molding tool. First draw the edge shape using curves, then rotate the shape and cap it to create a solid.Now perform the Boolean split between the handle and the base, then detach the surface. Next, copy the edge line, move the inner circle downwards, use the double rail sweep to generate the surface and combine it to obtain the base shape.Use the center point circle and rectangle tools to generate the button and indicator light shapes on the handle, extrude the solid and then perform a boolean split with the handle to get the handle shape and the indicator light.Use the Rectangle to create the runway circle and rotate it 45° to get the "x" below, then use the Trim tool to trim off the excess lines and combine them. After extruding the surface, use the Boolean split tool to split it to get the "x" icon.Now create the circular texture on the button. First abstract the structure line to get a button-sized circle, then generate a circle solid at the circle node, and use the Array Along Curve tool to make an array. Arrange the five columns in sequence according to the image and mirror them to get the desired texture. Finally, we use Boolean split to get the button shape.Chamfer the intersection of the button and the handle, and chamfer the intersection of the handle and the base.Use the curve to draw the fan shape, then use the XN tool to generate the surface, and array along the center point. The number of arrays here is 5. Adjust the fan blade position and extrude the fan blade solid.Check the model and chamfer it to complete the model.The next step is to render the product. First, divide the product into four layers, one for the orange object, one for the flesh-colored object, one for the metal connection, and one for the self-illumination. Then start rendering.First adjust the model position by aligning the model to the ground in the Advanced Options.Set the model materials to the model in turn. Note that you need to turn down the metallic shine of the metal joints in order to get a frosted look.Adjust the self-luminous material on the handle to the right intensity in accordance with the light, and choose white as the color.Set the setting options in the image to Press Exposure, High Contrast, and Photography.Change the background color in the environment settings. Use the straw tool to absorb the image color, turn down the brightness of one light in the HDR editor, hit the light on the hollow surface, adjust the shape of the light to rectangle, and then hit a main light on the left side of the product to make a shadow appear on the right side.Adjust the object position in the camera, lock the camera, and finish the rendering.Source: YBW
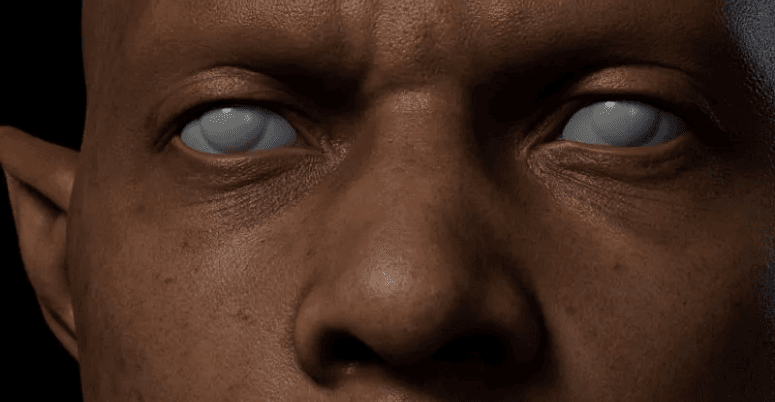
How to Use VFace and Make Effects in Arnold?
Arnold
In this article, Fox Renderfarm, the CG industry's leading cloud rendering service provider and render farm, will share with you how to use VFace and how to restore effects in the Arnold renderer. The author is CaoJiajun.Firstly I purchased some VFace materials from the official website to get the following files.We will mainly use the above files for this sharing, they are our main materials to make high quality details of the face. VFace provides 2 types of facial models, one for the head with open eyes and one for the head with closed eyes, choose one of them according to your needs. If you are doing a model that needs to be animated with expressions in post, I would recommend choosing the model with closed eyes, as the open eyes model will cause the eyelids to stretch when you do the blink animation. You don't need to worry about this for still-frame work.Let's start with the production process. It's actually very simple, wrap your own model with a VFace model through Wrap or Zwrap, then pass the map and finally render it in Maya or other 3D software. The process is simple but there will be a lot of things that need to be taken care of in there otherwise the facial details will not be rendered correctly.1 Model CleaningFirst we need to load the model provided by VFace into ZBrush and match it to our sculpted model.Then you can head into Zwrap or Wrap for wrapping.Lastly, the wrapped model is imported into ZBrush to replace the VFace model.In ZBrush we use the Project brush to match the face of the wrapped model more precisely to our own sculpted model, once matched you will have a model that matches your sculpted model perfectly, at this point we can go into Mari for the map transfer.2 Using Mari to Transfer the MapIn Mari we first set up the project, import our own sculpted model or the wrapped and matched XYZ model, then remove the other channels in the Channels and keep only the Basecolor channel, and we can customize the channels as we wish.What we see now is how the model looks when imported into Mari. At this point we need to set the custom channels DIFF\DISP\UNITY\ to import the VFace map.Firstly, the DIFF channel is set at the original size of 16k and the Depth is set at 16bit (later on there can be more color depth control and of course it can be set to 8bit). The key point is that when the color depth is set to 16bit or 32bit, the color space needs to be set to linear and 8bit to srgb.Keep the size of displacement map at 16k. I recommend setting the Depth to 32bit, as you will get more detail of displacement, and keep the color space linear, with Scalar Data ticked (as the displacement map is a color map with 3 channels of RGB, you need to keep the greyscale data).The blend map settings are the same as the color map, but Scalar Data also needs to be ticked (this map is used as a color mask for toning or as a weighting mask).Next we can use the object panel to append our own model in preparation for the transfer of the map.Right-click on any channel and select the Transfer command in the pop-up menu to bring up the menu for transferring the map.In the transfer menu select the channel which needs to be transferred in the first step, set the transfer object in the second step, click on the arrow in the third step, set the size in the fourth step and finally click on the ok button.I generally recommend passing one channel at a time as it is very slow and takes a long time to wait. For size I usually choose 4k for color, 8k for displacement and 4k for mixing channels. This step requires a lot of patience!VFace original effectThe effect after transferAfter the transfer we can export the map. The export map settings are shown in the figure. We need to pay attention to the color space setting (in the red box). The color space of the color channel is set to linear and should also be set to linear when exporting. The export of displacement and hybrid maps is a bit more unusual, as we set the color space to linear when creating the channel, but the export needs to be set to srgb, as both the displacement and hybrid maps are a combination of the 3 channels R,G,B to form a color map. Finally click the export button and it's done.VFace original color effectColor effects after exportingVFace original displacementEffect after exportIn short, your output map needs to be the same color as the map provided by VFace, either too bright or too dark is an error.3 Arnold RenderingDefault settingsAt this point we can go to Maya and render the VFace map we have created (we won't go into the lighting environment and materials here, we will focus on the link to the replacement map). First we import the passed VFace map and render it by default to see what we get. Obviously we get an ugly result, so how to set it to get it right?Here we add an aisubtract node (which you can interpret as a subtraction or exclusion node), because the default median value of VFace is 0.5 and arnold prefers a replacement map with a median value of 0. So we enter the VFace color into input1 and change the color of input2 to a luminance value of 0.5. This is equivalent to subtracting the 0.5 luminance info from the default 0.5 median luminance of VFace, and we get a displacement with a median value of 0.Median value 0.5Median value 0After setting the median we can add an aimultply node. This node can be interpreted as a multiplyDivide node, which has the same function as Maya's own multiplyDivide node and controls the overall strength of the VFace displacement. We can output the color of the aisubract node to the input1 node of aimultply and adjust the overall strength of the detail displacement of VFace by using the black, grey and white of input2 (any value multiplied by 1 equals 1, any value multiplied by 0 equals 0, all the colors we can see in the computer are actually numbers to the computer. We can change the value and thus the strength of the map by simple mathematical calculations, once we know this we can see why we use the multiplyDivide node to control the strength of the displacement).Next we add an ailayerRgba node. The R, G and B channels of the aimultipy are connected to the R channels of input1, 2 and 3 of ailayerRgba, and through the mix attribute of this node we can control the intensity of the displacement of each of the three VFace channels (R, G and B), and after a series of settings we can get a correct and controlled rendering of the VFace displacement.VFace-dispZBrush-dispVFace+ZBrush dispZBrush Export Displacement SettingsAlthough we have a correct and controlled VFace displacement result, it does not combine with the displacement we sculpted in Zbrush and we need to find a way to combine the two to get our final displacement effect.Here I used the aiAdd node to add the two displacement maps together to get our VFace displacement + ZBrush displacement effect (of course you can also use Maya's plusMinus node).It doesn't matter how many displacement map elements you have (such as the scar on the face, etc.), you can structure them through the aiAdd node to get a composite displacement effect. The advantage of making it this way is that you can adjust the strength and weakness of each displacement channel at any time, without having to import and export them in different software. It is a very standard linear process approach.Default effectAfter color correctionFinally we apply the passed color to the subsurface color, and by default we get a very dark color mapping, which is not wrong. The VFace default model will be the same color. We can correct the skin color by using the hue, saturation and lightness of the colourCorrect node. This is why I choose 16bit colors to bake with, so I can get more control over the colors and get a correct result after color correction (of course the current result is just a rough mapping, we can still do deeper work on the map to get a better result).As a powerful render farm offering arnold cloud rendering services, Fox Renderfarm hopes this article can give you some help.Source: Thepoly
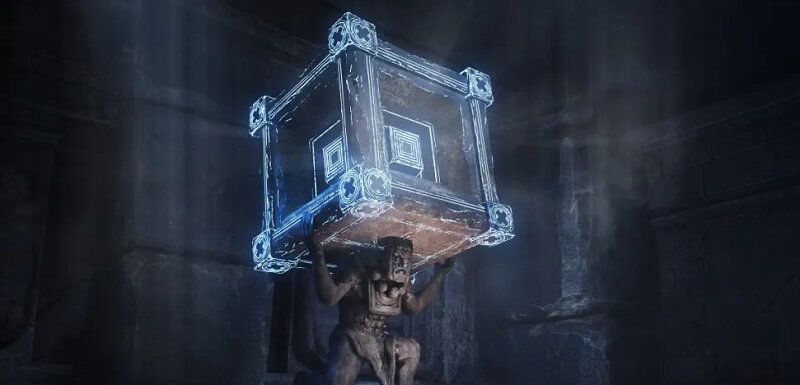
Create a Next-Generation Scene "Things From The Outside" with 3ds Max
3D Tutorial
In this article, Fox Renderfarm, the CG industry's leading cloud rendering service provider and render farm, shares a collaborative 3D scene tutorial, "Things From The Outside," produced by a team of 3D art and design students.This was the first time they used ZBrush in their production process, so they encountered a lot of difficulties and challenges. They chose to make a scene of an interior temple that was more complex in terms of sculpting but with relatively single materials, with the main purpose of increasing their ZBrush proficiency.The final result:Production FlowAnalysis of Original PaintingsThe first thing we did was to assign tasks. One person built the rough model, showed everything in the original painting with simple geometry, and then adjusted the scale. Then, based on the original painting, we analyzed the assets and divided the job. We assigned the tasks of each component of the original painting to each member of the group.When building the rough model, put the camera at the same angle as the original painting as much as possible. Building a rough model is about accurate proportions, so be sure to carefully find the right proportional relationship between each object and reproduce it.Making Mid-poly ModelWe used Substance Painter to create materials and divided the models that require sculpting in ZBrush into two categories: heavy and light sculpting. For some stones, we used 3ds Max to create a low-poly model before sculpting details in ZBrush. For irregular objects such as the white cube in the middle, we also used 3ds Max to build a rough model before creating a high-poly model in ZBrush.Making High-poly ModelAs shown in the above figure, two processes for creating high-poly models are demonstrated. The top stone model only requires sculpting of cracks and damage, while the bottom statue requires full sculpting. The process of creating high-poly models mainly involves refining rough blocky polyhedrons into objects that truly resemble the objects in the original painting. We encountered many difficulties during this process, but through continuous practice, we have improved our proficiency in using ZBrush.In my opinion, the most important thing in stone sculpting is to express the "mottled" traces of the stone. As a stone in the natural world, it must have been weathered by wind and rain, so a smooth stone will definitely give people an unnatural feeling.The method I used is the sculpting technique taught by my teacher. First, using the TrimSmoothBorder brush with a square alpha on the rough shaping can easily create a mottled surface. After that, reducing the brush size for detailing can result in a very "mottled" stone surface.As for human body sculptures, which are closely related to the human body, it was very difficult for us who have no background in art. We received several help from our teacher during the process, so that our "zero-based" group could sculpt a human body statue successfully.Making Low-poly ModelFor us, the creation of low-poly models is also a new topic in creating a next-generation scene because it requires topology. I think topology is a very demanding task because, besides reducing the number of faces as much as possible, the corresponding model also needs to be planned, which means considering which high-poly models need to be topologized into a low-poly one. Topologizing multiple high-poly models onto a low-poly one can not only save the resources of a model but also reduce unnecessary time waste during the later UV unwrapping and material making processes. There were two methods for topology: ZRemesher and Topgun, with the former being automatic and the latter being manual. However, according to our teacher, it was basically impossible for real company projects to use ZRemesher because automatic topology does not meet wiring standards. Therefore, for this scene project, we chose manual topology.After topology was completed, it was time to unwrap UV. However, since we were working together and dividing the work, there may be inconsistency in the size of UVs. Therefore, before unwrapping UVs, an important task needed to be completed which was to determine the pixel accuracy. By using the same pixel accuracy, it was possible to determine how many UV maps each team member needed for their respective creations, thereby ensuring consistent pixel accuracy throughout the entire scene.Thanks to the powerful real-time preview function of Marmoset Toolbag, all the models in this project were baked in it. If there were any normal distortions, they could be modified in real-time, which saved a lot of time checking for normal errors. Also, since many models were created through topology, a lot of time was saved in matching the high and low-poly model.Making MapsBefore making maps, our teacher told us that if there were a large number of models in the scene that had similar or identical materials, we could first create a basic smart material and then distribute it to team members for modification based on this material. This would help avoid situations where the overall color of the materials was inconsistent during final integration.The materials used to create this natural environment can be roughly divided into three aspects: basic materials, volume relationship, and details. The basic materials were uniform for all the group members, so what really needed to be worked on were the two plates of volume relationship and details.Regarding the volume relationship, it is better to highlight changes in light and shadow, so that the whole object does not look very flat. In terms of details, as the original scene is in a perennial moisture environment, so that there would be some moss in the location near the ground, and then the overall performance would be a little wet. In short, to try to meet the characteristics of the scene in the original painting.RenderingWe used Marmoset Toolbag to create the final rendered image. Marmoset Toolbag 4.03 has added support for ray tracing, making the lighting of the scene look very beautiful. Therefore, at the beginning, we did not consider additional lighting and relied too much on this feature. As a result, the entire scene rendered with large areas of dead black, while the bright parts were not emphasized. The reasons for this are firstly, the light and shadow relationships were not displayed clearly; secondly, cold light sources were not used to handle the dead black parts in the dark areas; thirdly, there were a large number of candles in the scene, but the candlelight was not simply completed by self-illumination and required additional fill light to achieve the desired effect. Of course, there may be many other problems as well. Finally, with the help of the teacher, our scene "regained life". The following two images can be seen for comparison.ConclusionThe above is the process and experience sharing of our group in making the next-generation 3D scenes. We have learned valuable things about collaboration and hope that these experiences can give you some help and encouragement.Source: Thepoly
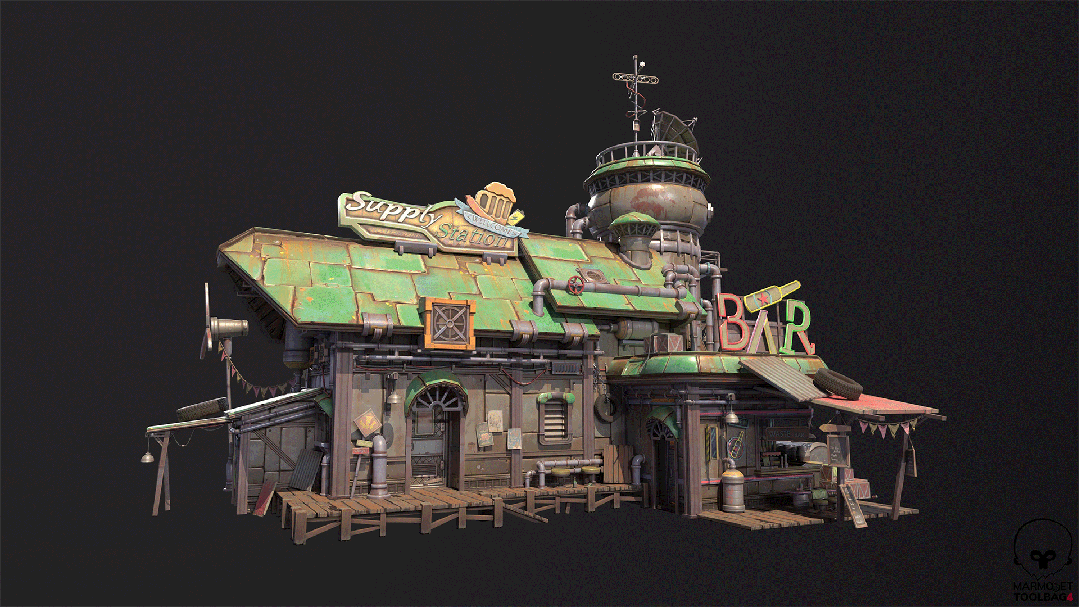
3D Tutorial: Next Generation Wasteland Building Production
3D Tutorial
As a leading cloud rendering service provider and render farm in the CG industry, Fox Renderfarm is here to share with you a production of a 3D stylised wasteland building from the author Xiaodenglong.Final result:I will provide a comprehensive breakdown of the design analysis, the next generation scene making process and the secondary conceptualisation.1. Design analysisArtistic stylePost-apocalyptic wasteland style: rebirth after destruction!BackdropNeon tubes glow faintly in a desert environment in a low-tech, battle-damaged, rusty wasteland world.In order to survive, people build shelters in a patchwork and random way, cleverly blending different objects together by fusing, twisting, fitting and mixing. As a result, the architecture of the wasteland buildings is crude, exaggerated in shape and relatively complex and mixed in design.Design elements: mainly consisting of broken and repaired metal sheets, pipes, wire mesh and nails, etc., with airbrushing to show the will to live.Setting: Lightly damaged, with most of the hard surface structure, suffering only slight breaks, and the core structure still intact.This backdrop setting creates a special environment for wasteland buildings, blending elements of destruction and rebirth.Status: Building in use.Colour scheme principle: large areas of low-saturated colors are used against partial high-saturated colors to enrich color variation and a strong sense of color blocking, which is very striking.ReferencesHere is part of it. A comprehensive search for reference will give a better senseof guidance and goal when it comes to production. References are very important!2. Analyzing &x26; PlanningSplitting of the buildingThe basic divisions are: tiles, walls, borders and frames, pipes, strips of wood, props, cables, fabrics, etc.Measurements: Units, Proportional, AccuracyMapping on the rough model:It is important to increase the rate of map sharing so that a set of maps can be flexibly adapted to more buildings, therefore the key point to consider in the design of a map is 'usability'.Rough modeling and mappingAs the original painting only has one angle, more thought needed to be put into the design of the other angles, which will be described in more detail later.It is particularly worth noting that in the design of tile and wall maps, avoid dividing them too evenly and consider the need for patchwork that applies to different sizes and widths.Design the maps of rough models with a focus on efficiency and quick communication of information.Quickly find your way through structure, colour, texture size, mapping accuracy, styling and more.As there will be a lot of shared elements in the building, you will need to think about how to use limited resources to do the patchwork work and ensure that you get good results.RefinementRough model mapping is essential to avoid many problems in advance and to ensure a more efficient and smooth production process.3. Mid-poly ModelNow we can concentrate our efforts on structural modeling. As the subsequent details of the model will be baked onto the plane, special attention should be paid at this stage to the correct representation of the hierarchical relationships.The correct way to express the hierarchy is as follows:Based on the representation of the real spatial relations of the objects, the first step is to deal with heights and undulations.The width of the slope is adjusted according to the change in height, for example, if the height is higher and the depth is greater, the slope can be adjusted to be wider as appropriate.It is also important to note the variation of the thickness of the gaps (structural lines) between the structures, which affects the expression of the hierarchy. Thicker gaps emphasize the width of the distance between the different structures and further emphasize the hierarchy.Good hierarchical relationships help to convey the sense of volume and space of objects more effectively and to obtain a good visual reading order.4. High-poly ModelAdd lines to some completed mid-poly models, and add detailed sculpting to metal tiles, walls, and wood, making them more rich and natural.Next, we will move on to the baking process, where we are using the standard PBR process.5. MappingIt was done in photoshop. Now we show the effect of the mapping drawn in photoshop.About the softwareThere is no good or bad software, I think it's important to combine the advantages of different software to improve efficiency.In terms of color processing in the maps: the sense of color blocking is very important! Especially for stylised mapping.It is not advisable to choose colors that are too highly saturated, but rather focus on the overall feel, cleanliness, sense of color blocking and brightness. Large areas are in gray tones and localized areas can be highlighted with highly saturated colors.Other maps are handled in the same way.6. Secondary ConceptionDuring the production process, I put a lot of thought into the composition. It would have been substantially more efficient if I had found a directly available reference, however, I still incorporated some of my own ideas and insights into it.CompositionAt the beginning of the production phase, no windmill element was included.It was later found that the overall composition became less complete with the removal of the windmill. In addition, the contour lines do not appear to be sufficiently varied.Visual balanceDuring the design process, one of the designs on the back gave me a headache for a while - the iron frame with the tyres.The previous design for this location seemed a little cramped and I later considered the relationship and balance between the architectural elements and used a patchwork of white metal walls and tyres. This not only adheres to the style of mixing and matching in wasteland architecture but also adds a touch of lightness to this area.In this way the design does not look dull but maintains visual balance.When dealing with the placement of architectural details, we have to take care that their heights are kept in balance, including the treatment of pipework. Also be aware of how to fill in the blank areas and guide the viewer's eye.Color balanceInside the bar, the colors of the tablecloths are not actually represented on the original paintings.I chose the same green as the color of the tiles for the tablecloth.I marked the green blocks as orange, and you can see that the distribution of the color blocks is sparse and staggered.Green can just echo the theme color, and vice versa, from the point of view of color distribution, may be a bit out of balance.This is what we have to consider later in the color matching.Processing of identical elementsFor example, the design of wood panels is often a bit boring if you just use the same elements side by side.Therefore, I added broken holes and wire to the wood panel. By doing so, not only will not destroy the original effect, but also add some detail changes and enrich the diversity of materials.Placement of propsDuring the design process, we can't ignore the placement of props.For example: the placement of chairs at the dining table.These seemingly insignificant details can actually reflect the state of use and traces of the bar, and can also smartly correspond to the background of the story.These details not only add a sense of realism to the building, but also create an immersive experience.Switching of visual guidanceVisual switching in architectural design is very important, especially during the day and night.In this case there are two plaques that clearly distinguish the atmosphere of day and night. When dealing with the details and placement of lighting props, I especially considered the conversion of visual guide lines to enhance the experience and perception of the viewer.Every good work requires a lot of thought. Although there are still some regrets in this work, I will summarize the experience and problems and enhance and improve it in the next work.We hope the sharing of 3D wasteland building can bring some inspiration to you. In the last step of the rendering process in producing 3D work, if you need to meet the deadline and speed up the rendering to deliver your project in time, try the super fast cloud rendering service offered by Fox Renderfarm. We offer a $25 free trial and have 24/7 customer service for you!Source: Thepoly
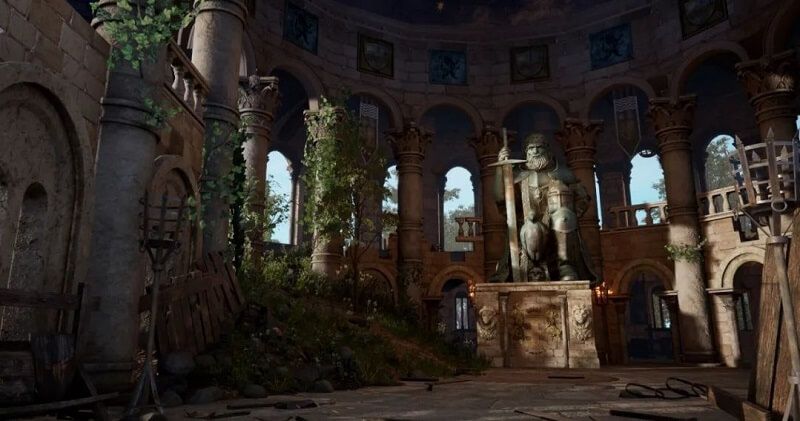
A Sharing of 3D Scene Reproduction from 'For Honor'
3D Tutorial
In this article, Fox Renderfarm, the CG industry's leading cloud rendering service provider and render farm, shares a 3D scene produced by a team of students working together, based on the Ubisoft's game "For Honor".Final result:1. Analyze Original Artwork and construct Rough SceneWe used a standard PBR production process for this case. In order to accurately restore the scene proportions, all team members conducted on-site inspections in the game. Afterwards, individual tasks were assigned to each person.To ensure that the proportions of the model are accurate, our team leader simplified the entire scene into basic geometric shapes and assigned these models to individuals as reference for scale.Rough scene model2. Making Mid-poly ModelCharacter sculpture: At the beginning, I was very confused because I had never dealt with character sculpture before. After consulting with my teacher, I got some directions. The idea was to start with a basic human model in ZBrush and pose it, then reduce the polygons and export it as a reference for building the equipment structure on the model in 3ds Max. The head, hands, feet, and equipment were all done separately. As for the head, I adjusted the face using a basic male head model in ZBrush, and created a rough model of the hair and beard using two basic spheres. Because I had no experience with ZBrush sculpting, I had to spend some time every day learning the basics, which made me the slowest member in the group's progress during the entire production process.Mid-poly modelSmall objects: The small objects were not complicated for me. I needed to refine the model structure based on the rough model. It was important to pay attention to the object's topology and always consider adding edges loop in high-poly modeling. During production, it was crucial to ensure that the size of the small objects was consistent with the rough model, otherwise the proportions in the scene would be incorrect. For some small objects, such as wooden planks, locks, and iron rings, it was only necessary to create two or three different models and reuse them repeatedly.Wall pillar: This part requires the use of four-way continuous patterns, which seamlessly connects all four sides and loops around. The low-poly walls can be directly textured using this method. I made a lot of mistakes at the beginning, but with the guidance of my teacher, I was able to correctly use ZBrush's Deformation -> Offset feature to create the correct four-way continuous patterns.The mid-poly model is just for transitional purposes, designed to facilitate the production of high-poly models with as much detail as possible. It's important to ensure that the various components can be interspersed rather than being created as a single object, as it would not only be troublesome but also make sculpting difficult.Mid-poly scene3. Making High-poly ModelI find it really challenging to sculpt the stone texture of a person. I thought about many complex techniques, but in the end, I realized that simplicity was the key. I approached the sculpture by working on each part separately, starting with the face. I searched for a lot of references, mostly of elderly men, as well as some images of muscles and bones.Since I wanted to create a stone statue of a person, capturing the subject's characteristics was essential. I pushed down the center of his forehead to give him a serious look. I made each facial feature three-dimensional, and since he appeared to be older, I carved deeper eye sockets and more pronounced cheekbones. The fabric carving was also quite challenging, but after studying and practicing, I got much better at it.Sculpting high-poly modelStone and wood: In this part, the team encountered some issues. Specifically, the wood texture appeared unnatural with no variation, and in some cases, the wood grain was even at an angle. Meanwhile, the stone was carved too softly without any layers. The best approach to solve these problems is to observe the small details that we often overlook in daily life, and then be more careful and patient when sculpting. It's essential to consider the intrinsic characteristics of the object and avoid over-sculpting just for the sake of it.Sculpting small objectsPillar pattern: With the guidance of our teacher, we learned to use grayscale images to create some decorative effects. By using the correct method, we were able to save a lot of time in the project.Pillar patternHigh-poly scene4. Making Low-poly ModelFor irregular models such as figurines, eagles, and skulls, we exported their high-poly models and imported them into TopoGun for retopology. The topology was manually sketched using high-poly models, and followed the structure points while maintaining low face counts. Whenever possible, the convex structures were topologized, while small details, such as dents and damage sites, were achieved using normal maps instead of actual topology. It is important to follow the original structure when doing topology! Due to our lack of experience, we ran into various problems during the topology process, but we were gradually progressing. Regular objects were created by adding and subtracting lines from mid-poly models in the early stages.Topology modelAfter completing the low-poly models, it was time to split the UV maps. This raised the question of how many textures and what size should be used. Since this was a personal project, we standardized our texture size to 1 m/512 pixels. We aimed to maintain consistent pixel density throughout the entire scene. For the figurines, I used four 4096 pixel textures, while over 30 textures were used for the whole scene. If any member failed to organize the files properly, it would cause difficulties during integration. Therefore, it is crucial to adhere to the standards when submitting the files.Next was time to bake the normal map. We chose to use Marmoset Toolbag for baking the normal map. Because the topology of the models was already completely matched during the process, there was no need to match the high- and low- poly models again. However, for regular models, the matching process should be done in 3ds Max. Then, separate the high- and low-poly parts and group them before importing them into Marmoset Toolbag for baking.Marmoset Toolbag makes it convenient to manually edit some flawed normal maps. During baking, we make sure that the wrapper completely wraps around the high-poly models. If the normal map has minor issues, they can be fixed in Photoshop. However, if there are major problems, it's necessary to backtrack and search for the reason, such as whether a smooth group was separated but the UV wasn't disconnected.5. Making MaterialOur approach to material creation is to first identify the object's color and texture, create its volume, add textures, and finally add details.To maintain a consistent material tone across the entire scene, we had one student create the base materials, establish the tone, and then export intelligent material balls for others to use. They could then add texture details that suited their own model structures based on the established tone.Effective material creation process requires collaboration and communication; working in isolation and obsessing over individual model details while neglecting overall effects and tonal consistency is problematic.Layering materials can create more intricate effects, so it is advisable to experiment with different combinations.6. RenderingWe rendered using Unreal Engine 4. As we were new to the software, the team leader learned the software while attempting to adjust the visual effects. When importing files from 3ds Max to Unreal Engine 4, the team leader discovered an Unreal Engine official importer plugin called Unreal Datasmith, which greatly facilitated our work progress by allowing us to import all models into Unreal Engine 4.The most significant challenge we faced during resource integration was not knowing which map corresponded to which model. Therefore, the team leader requested that each team member partition their own models and maps. For example, if two items shared a map, the map and items had to be screenshotted together, with the size of the map marked. Later we found out that material effects were inconsistent - they were either too dark or too bright, perhaps due to lighting issues.In Unreal Engine, the team leader made detailed partitions for each person's model maps and material ball files. Different folders were given different colors, making it more efficient to organize and replace files.ConclusionThe above is our experience sharing of the entire production process. In conclusion, I would like to say that the process is more important than the outcome. Due to our lack of experience, there were significant differences between our work and our desired results. However, we gained much from this process. We learned about teamwork, gained technical knowledge, and understood many life lessons. The scene project production process was a valuable lesson in our lives. Therefore, I just want to say that we are all the best!Source: Thepoly
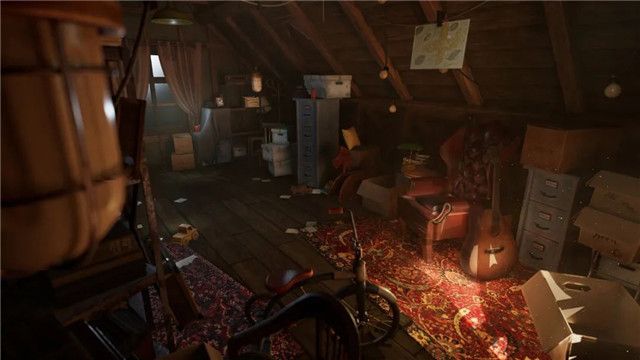
3D Tutorial: Creating a Next-Generation Scene 'Attic'
3D Tutorial
In this article, the leading cloud rendering service provider and render farm in the CG industry, Fox Renderfarm will present you with the production tutorial of a next-generation scene, "Attic," which was created through the collaborative efforts of a student team. Here are the specific production ideas and processes:Final result:1. Standardized ProcessesThe PBR workflow was adopted for this scene. After determining the theme, we first divided the scene assets into different areas and assigned them relatively evenly to each team member. Then we used 3ds Max to create a basic framework with simple geometric shapes to determine the proportions of buildings, roofs, and objects' positions and sizes. We continued to work on making mid-poly and high-poly models in 3ds Max, and then used ZBrush to perform detailed sculpting, such as creases and folds on sofas. The fabric was created using Marvelous Designer, and materials were made in Substance Painter and Photoshop. Finally, the scene was rendered in UE5.2. Create a Basic FrameworkFirst, use simple geometric shapes to build the overall structure of the house to determine the approximate placement of objects and their proportional relationships. This step plays a crucial role in the entire project, as it facilitates model replacement and project summarization.This stage focuses on achieving a grand effect, and it is necessary to repeatedly compare the original painting from multiple angles to avoid getting caught up in the placement of small objects and details and losing sight of the big picture. In addition, this stage also requires careful planning for the texture mapping accuracy of the models. We commonly use the method of placing small cubes with a size of 1m3 and a texture map resolution of 512x512 as a reference benchmark to confirm the accuracy.3. Make Mid-poly ModelsThe creation of mid-poly models is a fundamental yet vital step in the entire project workflow. By building the mid-poly model, we can essentially determine the approximate final effect of the model. Therefore, ensuring the accuracy of the mid-poly model's structure, proper wireframe layout, and correct differentiation of smooth groups are all crucial components of modeling work. Completing this step well can lay the foundation for the smooth progression of the subsequent workflow.4. Make High-poly and Low-poly ModelsConsidering that the model style in the project is generally regular, we chose to use spline and TurboSmooth in 3ds Max for our high-poly modeling process, followed by object edge damage sculpting in ZBrush to ensure higher production efficiency.For some cloth simulations, we choose to use MD software to obtain the high-poly model through object collision and then reduce its faces to obtain the corresponding low-poly model.The low-poly model can be reduced in face count while preserving the object's overall outline, and then the object's symmetry axis, naming, and materials should be linked and packaged. Otherwise, errors and objects flying around can easily occur when the project models are merged, resulting in additional integration work. Therefore, it is essential to keep one's files organized and standardized to minimize future complications.5. Make MaterialsMaterials are created in Substance Painter, and when working on materials, attention should be paid to objects within the same set in the scene, such as a desk and a bookshelf in the distance. Because these two objects happen to be made by different team members, communication during the material creation process is crucial to ensure consistency in color and texture. For example, if different shaped cardboard boxes in our scene are assigned to different students for modeling, these two members need to communicate well, or else the materials may appear jarring when placed together due to different material handling. Additionally, refinement and improvement of overall materials can proceed once the above issues have been roughly coordinated.The finished material textures are rendered in UE5.6. Lighting and Atmospheric RenderingRendering in UE is the biggest challenge in the entire stage. During this process, we enhanced the tranquility of the beam of light shining into the window and added texture details such as text on sticky notes on the computer desk, graffiti hanging on cardboard boxes and eaves, etc., to increase the storytelling and association of the image.During this process, we wanted to achieve a translucent and glowing effect for the window illuminated by light and asked our instructor for advice. We found that it was difficult to achieve the desired translucent material effect in UE5, where it was either fully translucent or semi-transparent. Finally, we chose to simulate the translucent material effect through dynamic jitter, and then reduced the jitter noise by increasing the rendering resolution. For some stubborn noise that couldn't be removed without affecting the overall image quality, we used Photoshop for modification to ensure the final result of the image was not impacted.In addition, we also added some particle effects to show the dust under sunlight and used glowing textures to create the scene outside the window. To handle the edge light of the curtains, we tried many different directions of light sources and adjusted the values of ray tracing to achieve the desired effect. Because the tone of the attic image became particularly warm after adding direct light, we chose to add auxiliary cold light to balance the picture. After taking high-definition screenshots, we modified the color balance, curve levels, etc. in Photoshop, and then imported the color card into the LUT filter function of the post-processing box to achieve the desired effect as much as possible.We also used volumetric fog in UE to create the effect of volumetric light formed by the light source shining into the room through the window.7. ConclusionThe above is a detailed description of our project production process. During this project, we learned a lot. This was the first time we had participated in a collaborative scene project, so we encountered many problems, including coordination between team members and related techniques for modeling and rendering. However, with everyone's efforts, these problems were successfully resolved. Although there are still many shortcomings, we have all put in our best efforts for this project. Finally, we hope that this sharing can bring inspiration and help to all model making enthusiasts.Source: hxsd
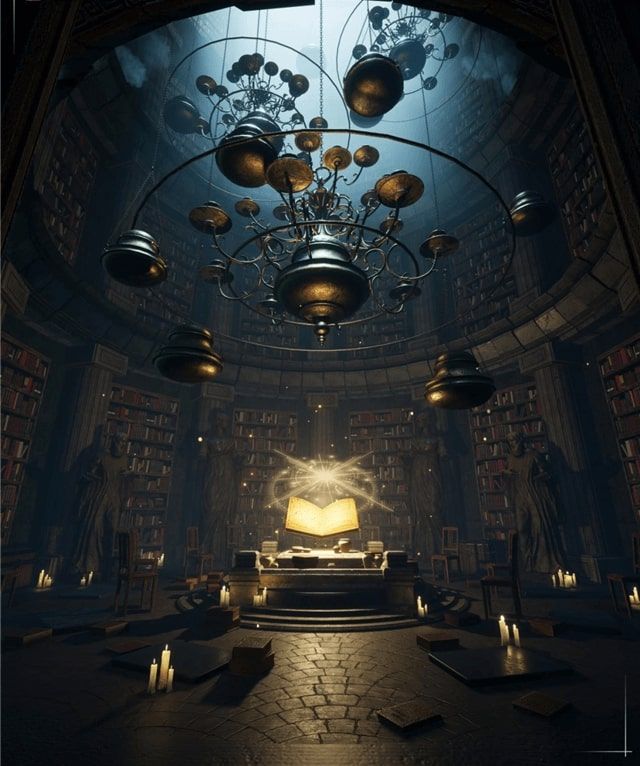
3D Tutorial of Next-generation Scene "Magic Book Room"
3ds Max Tutorials
In this article, as a leading cloud rendering service provider and render farm in the CG industry, Fox Renderfarm will bring you a tutorial on creating the 3D scene of the next-generation "Magic Book Room".1. Analyze and Build a Rough ModelThis is a case of PBR process, specifically using 3ds Max to complete the low-poly model, ZBrush to complete the high-poly sculpting, TopoGun for topology, Substance Painter and Photoshop for texture production, and finally using UE4 for rendering.To ensure that we can still achieve model proportion consistency after dividing the workload, we first built the overall scene in 3ds Max based on the original artwork as a reference for proportion. Then, after assigning each person with their respective models and props, we began the production process.2. Making Mid-poly ModelHouse structure: As the basis of the scene framework, the house is divided into three parts: roof, walls, and floor. By analyzing the original painting, the walls and floor are made of four-sided continuous materials, and the walls can be made into modular kits, which can then be reused in the scene.Props part: Scene props include two statues, a number of books, chairs and so on, of which statues, chairs, Roman columns and other props are sculpted in ZBrush, while books are classified based on material mapping, and a total of 18 books are produced to facilitate the future reuse.The process of making a mid-poly model is to refine and add more details on the basis of the rough model. In the pre-production, we should analyze what models need to be sculpted and topped, and what models can be obtained from the low-poly model by reducing the line in the mid-poly model. Pre-production analysis and planning can greatly improve the efficiency of our production.3. Making High-poly ModelThe production of the high-poly model is relatively calm, everyone is doing their own work in a step-by-step manner. The rough model made at the beginning is convenient for the present scale reference, so it is smooth to adjust the scene.Sculpting of statues:Sculpting of props:In order to better reflect the texture of the wooden chair, the wood grains on them were all carved by me one-by-one. I also sculpted the Roman columns, treasure chests, lamps and other props.4. Making Low-poly ModelIn the early stage, we analyzed the assets and found that only two statues needed to be topologized, the low-poly model of the remaining props could be obtained by reducing the line of the mid-poly models. Topping the low-poly model is a simple but patient job. There are several points to note in the process of topologizing statues:(1) Control of model face;(2) How to layout wiring in a reasonable way, and whether some details need to be topologically designed;(3) Whether the wiring density is reasonable;During the low-poly topology phase, there are not many difficulties encountered. We made textures with a standard of 1m3/512 pixels and finally planned the texture reasonably according to the preset pixel density. Then we performed UV unwrapping and layout. During this process, some models had seam problems, but we were able to locate the issue - it was due to some areas of the model not being disconnected from the smoothing group in the UV. When placing the UV, it is important to make full use of the UV space to avoid wasting resources, and further UV rework may be required in the future.Next is to bake the normal map. We matched the high-poly and low-poly models in 3ds Max, and then kept a certain distance between all models to avoid overlapping when baking. If there are issues with the baked normal map, we use Photoshop to repair it. Throughout the baking process, we did not encounter major problems, so any necessary modifications in Photoshop were minor.5. Creating Textures/MaterialsWhen making materials, it is important to focus on the overall volume first before adding the finer details. By "volume," we do not just mean that the material should have a three-dimensional appearance under lighting conditions, but rather there should be a sense of volume even in the absence of lighting effects, through the use of color and shading. The addition of dark tones and textures will further enhance the sense of volume in the model. Finally, a sharpening filter can be applied to make the details more visible, resulting in a material that has a true sense of depth under lighting effects.6. RenderingAfter meticulous file organization, we also standardized the naming of models, material balls, and textures, which made our work much easier when we entered the UE4 engine. After all the preparation work was completed, we began to place the models, add lighting and special effects, and finally set up the camera for rendering. During this process, a lot of time was spent on lighting, and it was difficult to achieve the desired effect in the combination of model materials and lighting. Finally, the problem was solved by using the lighting channel in UE4.Final result:ConlusionThe above is our experience and tutorial sharing on the entire production process. The experience of this month and a half of production has benefited us greatly. We not only consolidated the production process but also learned many production experiences and supplemented previous knowledge. Although we encountered many difficulties during the process, when the final product was completed, we felt that all the previous efforts were worthwhile.Source: ZCOOL
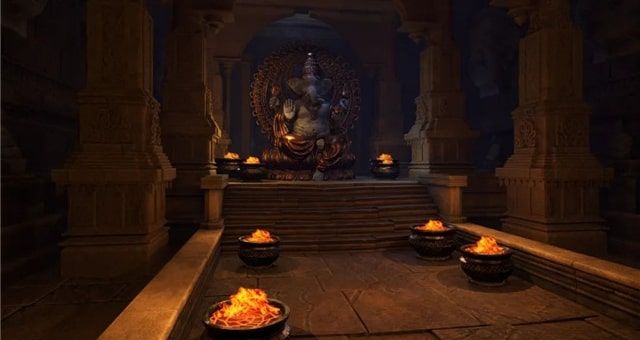
3D Tutorial of Making 'God Statue Corridor' Scene
3ds Max Tutorials
In this article, Fox Renderfarm, the CG industry's leading cloud rendering service provider and render farm, will bring you a tutorial on making 'God Statue Corridor' scene created by a team of students of 3D games models.Analyzing Original Painting &x26; Making the Basic ModelsFirst we analyzed the original painting, here we determined the length and width by checking the size of the original painting, and found the relationship between the location of the objects in Photoshop. Then we used the viewport protection frame and camera tools in 3ds Max to continuously refine the rough model's general shape, and used simple geometry to determine the model's location and size.Making Mid-poly ModelsAfter determining the large scale of the scene, we split the scene into various parts according to the size and complexity of the model. We divided the whole scene into four parts: the main statue, the ground and steps, the side walls and reliefs, and the column and beam patterns, after which we started working.God statue part: This part was the biggest difficulty for us who had almost no experience in ZBrush. As the visual center of the whole scene, we felt that it was important to ensure the integrity and coordination of the god statue and the base. Therefore, although the workload of the posterior high-poly model sculpting is heavy, we still decided to let the same person be responsible for the whole part of the god statue.Ground part: This part was a large area, but the models of bricks, steps and fire pits could be reused a lot. As long as the carving and material of the stone bricks were perfected,we could get a good result in the end.Side walls part: In this part, the wall was made in the same way as the floor, but with some additional figurines and Buddha head decorations. In the discussion and analysis, we found that these decorations were also important for the display effect in the post-rendering, so this part also became the focus of production.Column and beam part: The column is not a small part of the scene, it mainly shows the pattern and reliefs on the column surface. The modeling of this part was not very difficult, but we put a lot of effort on the material production and volume performance in the later stage.In the process of making the mid-poly model, we needed to perfect the details of the model and control the scale. We also put a lot of effort into the wiring, which facilitated the addition of lines and sculpting of the high-poly model later. Since this was a multi-person co-production, so in order to ensure that the scene would not lose its integrity, we integrated all the models after we finished our job every day and checked them to ensure that the overall scale size would not be wrong.Making High-poly ModelsSince we had almost no experience with ZBrush sculpting before, we were very apprehensive when we started to sculpt the high-poly model. But to our surprise, the production process was very smooth and the final result of the sculpting of high-poly model was good.During the process, we had a lot of experience sharing about sculpting, discussing mainly the categories of different types of structures, such as brick type and statue type. The purpose was to ensure the same or similar structures were carved with roughly the same accuracy and to ensure the coordination of all parts of the scene. At the same time, for some details of sculpting, such as cracks, breaks, bumps and undulations, we exchanged and shared some experiences on the use of brushes, and learned from each other's brilliant spots to improve our personal responsible parts.Making Low-poly ModelsIn this part, the complex structure was mainly topologized using TopoGun.We quickly got the low-poly model of the model with simple structures by matching the high-poly and low-poly models. For complex models such as statues and Buddha's head, we got the low-poly model by manual topology. This process was relatively simple and required patience and control of the smoothness of wiring.Making the MaterialsIn addition to making the texture of different materials, we also wanted to strengthen the sense of volume of the model. Moreover, since the materials were made by four people, each person made the same material in a different way, then the final performance would be deviated, resulting in an abrupt and uncoordinated effect of the scene. So in order to ensure the uniformity of the material performance, we increased the frequency of checking during the production process. We mainly standardized the inherent color, roughness, and metallicity of similar materials, as well as sharing our experience with each other on some details, such as the selection of miscellaneous colors for rocks.We strengthened the light and dark parts, enhanced the volume and top-bottom relationship of the model, and adjusted its roughness to make the model material more harmonious and natural. After that, we painted the texture and details of the material to make the story of the model as perfect as possible.RenderingWe used Marmoset Toolbag for the final rendering, restoring the atmosphere of the scene by adding warm and cold lighting, setting the fog, and enhancing the performance of the visual center. Also, the highlights and the firelight spreading to the surrounding area should be performed naturally.Finally, the organization of the files should be carried out with strict specifications, from the naming of the files to the organization of the models. During our cooperation, the unified file naming and cleanly sorted model files significantly improved the work efficiency.Final result:The above is the tutorial and sharing of the process of making this God statue scene.Source: ZCOOL
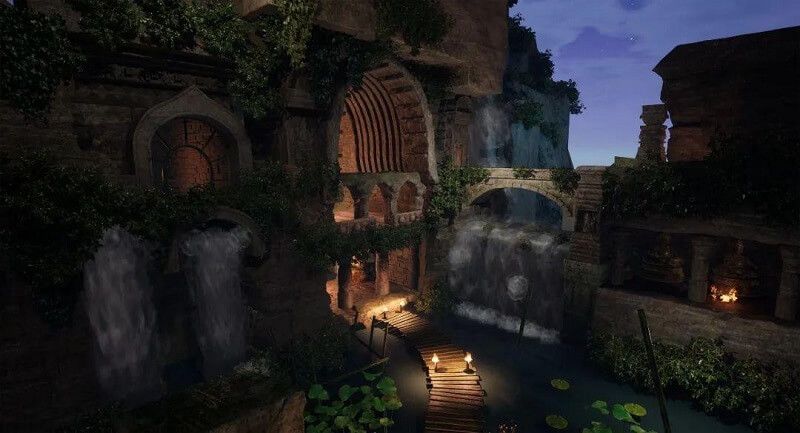
3D Tutorial: "Water Temple" Scene Production
3D Tutorial
In this article, Fox Renderfarm, a leading cloud rendering service provider and render farm, brings you a collaborative 3D scene "Water Temple" created by four students. This project was inspired by artist Sergei PaninPRO.Final result:1. Analyze Original Painting and Asset AllocationThe entire scene is a PBR process case. First, we used 3ds Max's gray box to build the overall framework of the entire scene, in order to ensure that the overall proportion structure is correct. Then, we evenly distributed various asset models inside the framework to each team member, allowing them to improve the details of their responsible models, and then used ZBrush to complete the refinement of the entire high-poly model. We used the Decimation Master and TopoGun 3 Beta in ZBrush for retopology. Afterwards, we used Marmoset Toolbag 4 for high-poly and low-poly matching, and the resulting low-poly model was taken into Substance Painter to complete material production. Finally, we used UE4 to render the images.2. Making Mid-poly ModelThe production of the mid-poly model involves continuous modification and improvement based on the white-box model. During the early stages of production, various issues such as wiring, sculpting, topology, and which models can be reused to avoid wasting resources must be considered. Since the objects in our scene are made separately, after the team members modify their models, the team leader needs to constantly control the overall proportion of the scene on a large scale. During the production process, the model is continuously refined to achieve a general appearance with reasonable and symmetrical wiring, which is convenient for subsequent high-poly carding and sculpting. And individual components and the overall effect are repeatedly observed, while the proportion size is continuously adjusted to ensure that the model's proportions are not disordered when integrated later.3. Making High-poly ModelThe high-poly modeling process went relatively smoothly, and everyone was working step by step on their own tasks. Because the low-poly model served as the basis for proportion, everyone did not encounter many problems when integrating the scene.The entire scene was built up from stacked boxes, and there were no major issues in constructing the low-poly model. The key focus was on high-poly sculpting to recreate the mysterious atmosphere of the ruins, which required a significant amount of stone sculpting. The sculpting approach aimed to ensure uniformity of the stone material and enhance the surface details. Due to a lack of experience, the sculpting process was initially slow, and some patterns could not be reproduced. Some of the methods used for detailing may have been wrong. Finally, with the guidance of the teacher, a method using grayscale maps was found, which saved a lot of time. First find suitable grayscale maps and then generate masks using ZBrush.High-poly models were used for rendering the scene, and to ensure a good rendering effect, we decided to duplicate and place models of flowers, grass, and other vegetation that appeared repeatedly. Finally, we rendered the scene and set up the lighting using Marmoset Toolbag for easy observation of the overall effect.ZBrush sculpting4. Making Low-poly ModelSince most of our models were sculpted, the face count is usually very high. When creating low-poly models, reducing the face count is a very important task that must be prioritized. Therefore, we first used the Decimation Master in ZBrush to perform an initial reduction of the face count for our high-poly models.The purpose of this retopology was to reduce the extremely high number of faces in the high-poly model all at once, while also preserving the structure and preventing deformation during the reduction process. However, one disadvantage is that after using the decimation master to reduce the face count, the topology becomes very messy. Therefore, it is necessary to do a secondary retopology in TopoGun 3 Beta while organizing the topology. Extra topology should be added to areas with important structures, prioritizing structural integrity.In areas without structure or where there is only one flat plane, such as the following stake, the topology can be simply optimized to further reduce the face count while optimizing.The retopology process is time-consuming, and if one is impatient, not only will the face count be reduced poorly, but it may also cause issues with the low-poly model. Therefore, it is important to have a lot of patience when it comes to retopology.5. Making MaterialFor materials, we used Substance Painter for sculpting and texturing. Since this was our first time collaborating to create materials of scenes, initially there were no problems when looking at each person's materials. However, after merging them together, we found issues with the differences in color and style between the materials not matching each other. Afterwards, we discussed and determined the color schemes and textures together, which made the material creation process much smoother.6. Final RenderWhy did we choose to render in UE4 instead of Marmoset Toolbag? Because it's more convenient to use the waterfall, river resources, and arrange some vegetation in UE4. Additionally, texturing in UE4 is also faster.After all preparations were completed, the only thing left was file integration. Everyone had been naming and organizing files since the beginning, so the final integration stage went relatively smoothly. Although there were some minor problems, they were all caused by models not being named clearly enough, so it's important to pay attention to proper file naming. The remaining work involved leisurely placing textures, arranging vegetation, and setting up lighting. One point to note about lighting is not to let the scene have areas that are completely black, as this will affect the overall effect of the scene.7. ConclusionThe above is our production process for the entire scene. This experience is truly invaluable, and we hope that everyone can cherish this process. When encountering difficulties or differences of opinion, don't give up. Keep working together to solve problems, because your persistence will definitely lead to better results.Source: Thepoly
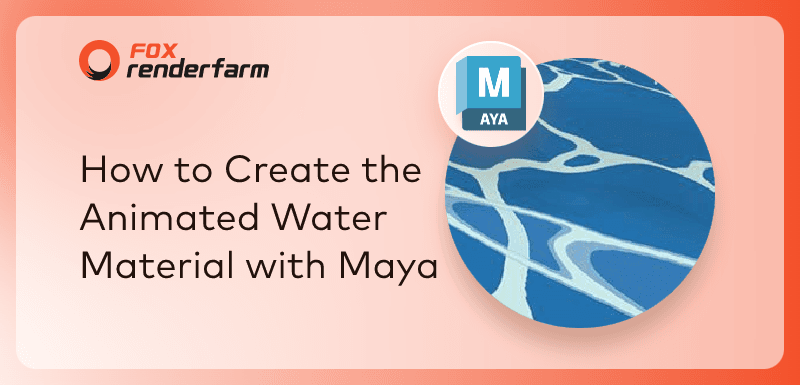
How to Create the Animated Water Material with Maya
Maya
As a leading cloud rendering service provider and render farm in the CG industry, Fox Renderfarm has organized a Maya tutorial article for you. Next, let's see how to use Maya to create the animated water material.The animated water will look like the following image:Image from the InternetMaking ProcessFirst, create a plane and assign it Ai Standard Surface.Add a Noise node to Color.Replace Noise Type with SpaceTime and adjust the Threshold, Amplitude, Ratio and Frequency Ratio parameters as shown on the screenshot.Then set the Time parameter to 0 at frame 1 and 1.45 at frame 200. Now play the timeline, which shows a dynamic Noise effect.Once that's done, adjust Depth Max to 5 and Frequency to 9.5.Find Effects and click Insert at Color Remap.Change the color of these two dots separately.Add another color and adjust the positional spacing of these 3 colors.For optimization, change the Type to Tartan Ramp, and adjust the U Wave and V Wave values to 0.091 and 0.201 respectively. Finally, adjust the spacing of the 3 colors appropriately and done.The above is the process of making animated water material in Maya. Now try it yourself.Author: JiweiSource: Thepoly
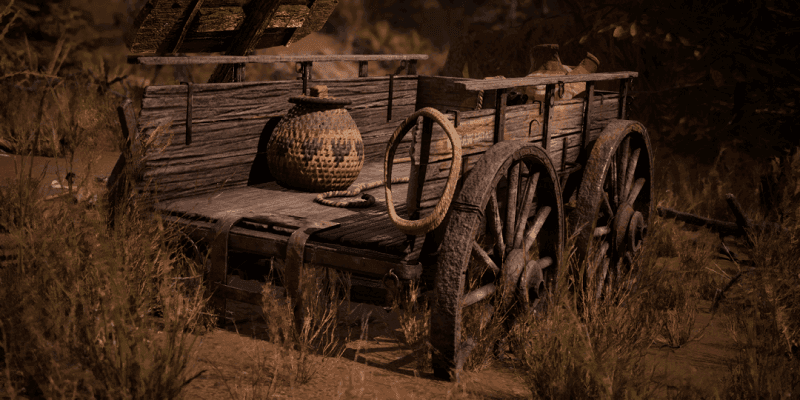
3D Tutorial: The Production Process of 'Medieval Abandoned Cart'
3D Tutorial
In this article, Fox Renderfarm, a leading cloud rendering service provider and render farm in the CG industry, will share the process of creating the "Medieval Abandoned Cart" 3D scene. This scene was meticulously crafted by a student team over two months. Let's explore the final outcome:Analyzing the Concept Art and Constructing the Rough ModelThis is a case study of the PBR workflow. The low-poly model was created in 3ds Max, while the high-poly sculpting and face reduction were done in ZBrush. Texture creation was accomplished using Substance Painter and Photoshop. Then, the final rendering was carried out in Unreal Engine 5.The scene primarily features the wooden boards on the carriage, a partially damaged piece of wood at the front of the carriage, along with items on the carriage, and other miscellaneous components.Creating Mid-poly ModelsMain Structure: The scene extensively utilizes wooden boards, temporarily substituted by boxes. The carriage wheels and other objects are also initially shaped using boxes or cylinders, later to be sculpted in ZBrush. Details include ropes, screws on the carriage, and iron chains. The rest has been sculpted to facilitate the later material creation.The process of creating the mid-poly model involves continuous refinement and the addition of richer details based on the rough model. During the early stages of production, it is crucial to identify which models require sculpting and face reduction to obtain the low-poly model. A well-planned early stage significantly enhances the overall efficiency of the production process.Creating High-poly ModelsThe primary sculpted elements include wood, cans on the carriage, and sacks. Sculpting wood with ZBrush is rather common and essential while creating scenes like this, and it is also crucial to maintain the overall shape after sculpting the mid-poly and high-poly models.Wooden Board Sculpting: The majority of the scene consists of wooden boards, starting with a basic box for sculpting. I sculpted a total of five wooden boards, reducing visual repetition through flipping, symmetry, and randomization. During the sculpting process, I first lightly outlined the wood grain and planned the major cracks using the Dam Standard brush. More details were also added to the deeper crack areas. Subsequently, I used the TrimNormal brush to flatten the surface, adjusted the edges, and incorporated alpha to enhance finer details.Sack Sculpting: Utilize the Dam Standard brush for sculpting the major details, and use the Standard brush to create natural protrusions and indentations. Enhance finer details by incorporating alpha during the sculpting process.Creating Low-poly ModelsBased on the early stage analysis of the concept art, only the sacks on the carriage need face reduction. The wooden parts can utilize the low-poly model extracted using the face reduction method, while the remaining sections can obtain the low-poly model through mid-poly face reduction. Overall, reducing the face of the low-poly model is a straightforward but patience-demanding task.Points to consider:1. Make sure the model's face count is manageable.2. Rational wireframe layout, determining whether certain details need to be refined.3. Proper density of the wireframe. Use a standard of 1m³/512 pixels for texture creation. Models with semi-transparent and transparent elements like glass candles should have a separate texture for later rendering.In this scene, three 4096-resolution were used, guiding the UV unwrapping and arrangement. Next, in 3ds Max, align the high and low-poly models and ensure some distance between them during baking to avoid overlap. If any issues arise with the baked normal maps, return to 3D modeling software like Blender and Photoshop for normal map correction.Creating TxturesAfter following the teacher's demonstration, I've acquired a more efficient process for material creation. In the initial stages, I use generator filters to establish volume. I downloaded some suitable textures from Bridge and overlay them with the textures provided by Substance Painter (SP) to enhance details. Finally, I adjust the color using HSL filters, apply sharpening, and strengthen the overall details in the material.RenderingBefore rendering, it's crucial to organize files and ensure consistency in the naming conventions of models, material balls, and textures. Standardizing the workflow reduces unnecessary complications. Once all preparations are complete, I import the models into the engine, perform some basic scene assembly, set up lighting, position cameras, and initiate the rendering process.The above is a sharing of the production process of the "Medieval Abandoned Cart" 3D scene. If you encounter issues during rendering, consider trying Fox Renderfarm's cloud rendering service. It can assist you in safely and quickly completing the rendering of your work.Source: Thepoly
Recommended reading
Top 9 Best And Free Blender Render Farms of 2025
2024-12-30
Revealing the Techniques Behind the Production of Jibaro "Love, Death & Robots", Which Took Two Years to Draw the Storyboard
2025-02-10
Top 10 Free And Best Cloud Rendering Services in 2025
2025-03-03
Top 8 After Effects Render Farm Recommended of 2025
2025-02-10
Top 5 Best and Free 3d Rendering Software 2025
2025-02-10
Shocked! The Secret Behind Using 3D to Make 2D Animation was Revealed!
2025-02-10
How to Render High-quality Images in Blender
2024-12-04
Easy Cel Shading Tutorial for Cartoon in Blender Within 2 Minutes
2025-02-10
Partners